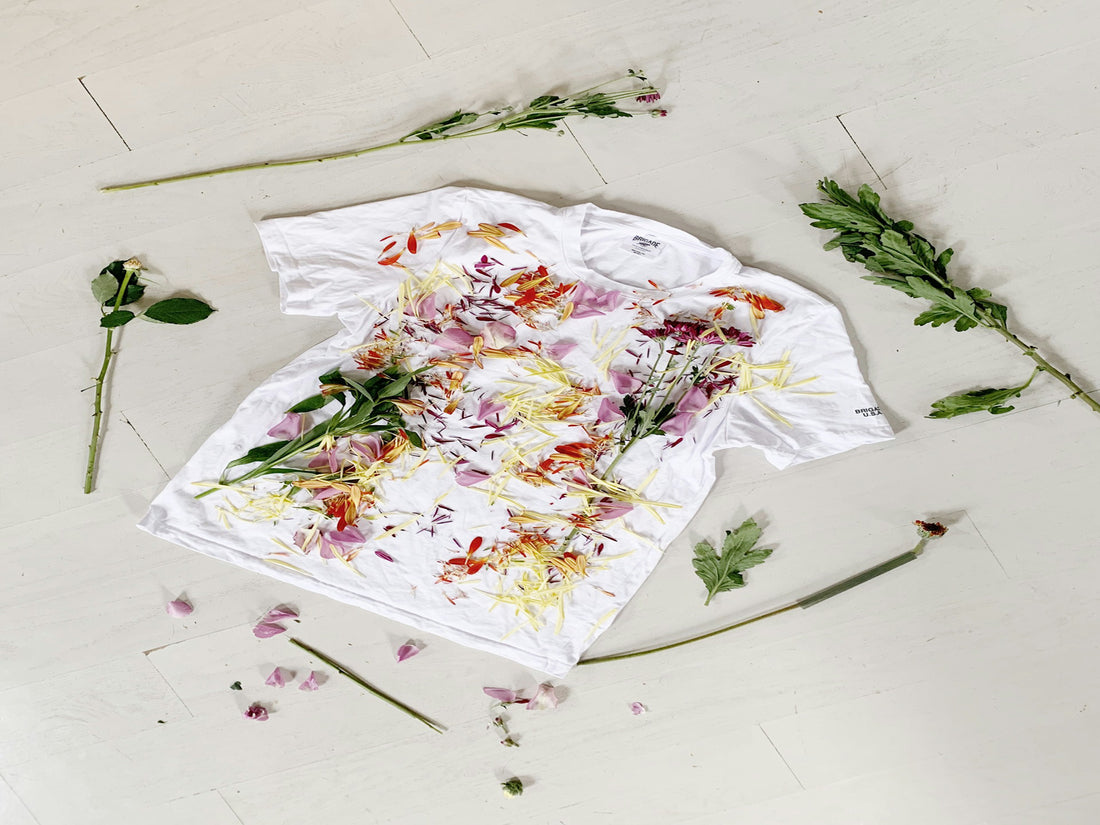
Can You Sublimate on Vinyl?
Share
Sublimation and vinyl are essential in the world of printing and design, finding their place in everything from stylish clothing to cozy home décor.
In this article, we'll dive into the exciting possibility of merging these two techniques—bringing sublimated designs to life on vinyl.
Our goal is to harness the bright, long-lasting qualities of sublimation along with the adaptability of vinyl to spark creativity and produce top-notch results.
Key Takeaways
- Use specially coated vinyl that can withstand the high temperatures of sublimation for compatibility and effectiveness.
- Sublimation embeds dye into the vinyl, producing vibrant, durable images resistant to fading and peeling, unlike vinyl heat transfer which may degrade faster.
- Sublimation on vinyl demands significant investment in specific equipment like printers and presses, and mastering the technique involves a steep learning curve.
- Used in various industries including fashion, home decor, and automotive, sublimation on vinyl supports extensive customization and creative applications.
- Requires well-ventilated areas and protective gear to handle high temperatures and potential fumes, with regular equipment maintenance for safety and efficiency.
Sublimation: The Science Behind the Print
Sublimation is a scientific process where a solid turns directly into a gas, bypassing the liquid state—a phenomenon known as phase transition.
In printing, this involves using special inks printed on transfer paper. When heated to about 400°F (204°C), these inks vaporize into gas, permeate a polymer or polyester-coated material under pressure, and solidify within the fibers as they cool.
This results in prints that are vibrant, fade-resistant, and crack-free, making sublimation ideal for high-quality visual applications like fabric and ceramic photographic prints.
Vinyl: Durability and Versatility
Vinyl, or polyvinyl chloride (PVC), is a versatile synthetic polymer that becomes malleable when heated and solidifies upon cooling.
In the design and print industry, vinyl varies in thickness and flexibility to suit different uses, such as durable flooring or flexible decals.
Known for its durability and resistance to UV light, moisture, and wear, vinyl is excellent for both indoor and outdoor uses, including car wraps and signage.
It can be printed on using techniques like digital inkjet, screen printing, and heat transfer.
How to Sublimate on Vinyl
Materials Needed
To begin with sublimation on vinyl, the right set of tools and materials is essential. Here's what you'll need:
- Sublimation Printer: This specialized printer uses sublimation inks and is capable of producing high-resolution images.
- Sublimation Ink: These inks are designed to turn from solid to gas under heat, embedding into the substrate.
- Heat Press: A machine that applies heat and pressure, essential for the sublimation process.
- Suitable Vinyl: Not all vinyl is appropriate for sublimation; look for vinyl specifically marked as suitable for high temperatures.
- Heat-Resistant Tape: This tape withstands high temperatures without melting, used to secure the transfer paper to the vinyl.
- Silicone Mat: Helps protect the vinyl and heat press, and ensures even heat distribution during the sublimation process.
Preparation
Proper preparation is key to ensuring that the sublimation process goes smoothly, and the final product meets quality expectations.
- Select the Right Vinyl: Ensure the vinyl is labeled for sublimation. This vinyl is usually coated with a special layer that can withstand the sublimation temperature and allow for proper dye adhesion.
- Cleaning the Vinyl: Before you begin, clean the surface of the vinyl thoroughly to remove any dust, grease, or other contaminants. This can be done with a soft cloth and isopropyl alcohol. Ensure the vinyl is completely dry before proceeding.
Sublimation Process
Printing the Design
- Use a graphic design software to create or import your desired image.
- Ensure the design is mirrored before printing, as it will be placed face down on the vinyl.
- Print the design using a sublimation printer onto sublimation paper, ensuring that the printer is set to the highest quality setting for clarity and color accuracy.
Preparing for Heat Transfer
- Preheat the heat press to the recommended temperature for vinyl, usually between 380°F to 400°F (193°C to 204°C).
- Place the silicone mat on the bottom plate of the heat press to prevent heat damage to the vinyl and ensure even heat distribution.
Transferring the Design
- Place the vinyl on the silicone mat inside the heat press.
- Position the printed design face down on the vinyl and secure it with heat-resistant tape to prevent any movement during the transfer.
- Cover the design with a Teflon sheet or another protective layer to prevent any ink from transferring to the heat press.
- Press the vinyl according to the heat press manufacturer’s instructions, typically for about 30-45 seconds under firm pressure.
Cooling and Finishing
- Once the time is up, lift the heat press and carefully remove the Teflon sheet.
- Allow the vinyl to cool slightly before peeling off the sublimation paper. This should be done gently to ensure the design has fully transferred and to prevent any smudging.
- Inspect the vinyl for any issues and allow it to cool completely.
Essential Precautions for Sublimation on Vinyl
1. Monitor Temperature and Time Closely
Accurate temperature control and timing are crucial in the sublimation process. Here’s how to manage these elements effectively:
- Use a Reliable Heat Press: Invest in a heat press with accurate temperature settings and a built-in timer. This will help maintain the necessary heat level and ensure that the vinyl is not exposed to heat for longer than required.
- Regular Calibration: Regularly check and calibrate your heat press to ensure that it provides accurate temperature readings. This prevents overheating, which can damage both the vinyl and the sublimation print.
- Adhere to Recommended Settings: Different types of vinyl may require different temperatures and pressing times. Always follow the manufacturer's recommendations for the best results.
2. Use a Protective Barrier
A protective barrier between the vinyl and the heating element can prevent damage to both the material and the device:
- Teflon Sheets: Place a Teflon sheet over the vinyl during sublimation. Teflon is heat-resistant and will protect the vinyl surface from direct contact with the heat press, reducing the risk of melting or texture changes.
- Silicone Pads: Using silicone pads beneath the vinyl can help distribute the heat evenly across the material, preventing hot spots that could cause warping or inconsistent coloration.
3. Ensure Your Workspace is Well-Ventilated
Sublimation involves the release of gases as the dye transitions from solid to gas form. Proper ventilation is important for safety, particularly in enclosed spaces:
- Ventilation Systems: Ensure your workspace is equipped with adequate ventilation systems to extract any fumes produced during the sublimation process. This is important not only for personal safety but also to maintain a clean and clear working environment.
- Use of Respiratory Protection: In smaller or less ventilated spaces, consider using respiratory protection such as masks designed to filter out fine particles and gases.
- Regular Air Quality Checks: Maintain the quality of air in your workspace by regularly checking and cleaning ventilation systems, and keeping doors or windows open when possible to allow fresh air circulation.
Additional Safety Tips
Here are a few more safety precautions to consider when sublimating on vinyl:
- Wear Protective Gear: High temperatures are involved in sublimation, so it’s wise to wear heat-resistant gloves and protective eyewear, especially when handling the vinyl immediately after pressing.
- Keep a Fire Extinguisher Accessible: Always have a fire extinguisher nearby. Although rare, accidents involving electrical and heat-generating equipment can occur.
- Educate Yourself and Staff: If you're working in a commercial setting, ensure that all operators are trained on the proper use of sublimation equipment and are aware of safety procedures.
By taking these precautions, you can safely and effectively use sublimation techniques on vinyl, creating high-quality, durable designs while maintaining a safe working environment.
Examples of Sublimation on Vinyl
Fashion and Apparel
Sublimation on vinyl is extensively used in the fashion industry to add colorful and intricate designs to various items. Here’s how it’s applied:
- Customizing Bags: Designers use sublimation to add personalized artwork, logos, or patterns to synthetic fabric bags.
- Shoes: Vinyl parts of shoes, such as panels or straps, can be sublimated to feature unique designs that stand out.
- Jackets: Vinyl patches or sections on jackets can be enhanced with sublimated graphics, often seen in sportswear or high-fashion contexts.
Home Decor
In the realm of home decoration, sublimation on vinyl allows for high-quality and resilient design applications:
- Wall Decals: These are popular for adding personal flair to home interiors. Sublimation ensures that these decals are vibrant and can feature detailed designs.
- Floor Tiles: Vinyl floor tiles can be customized with sublimation to create unique, durable flooring options that maintain the design integrity even under foot traffic.
Automotive Applications
The automotive industry benefits from the durability and quality of sublimated vinyl, used in both interior and exterior applications:
- Decorating Car Interiors: Dashboard pieces, door panels, and seat covers can be sublimated with custom designs to enhance the vehicle's aesthetic or branding.
- Exteriors: Vinyl car wraps are sublimated to produce detailed and durable designs for both personalization and commercial advertising on vehicles.
Challenges and Limitations
Compatibility of Vinyl with High Temperatures
Not all vinyl is suitable for sublimation; it must be able to withstand high temperatures without melting, distorting, or releasing harmful chemicals.
The need for specialized vinyl that can endure the sublimation process can limit the availability and variety of materials, potentially driving up costs and reducing flexibility in material choices.
Substantial Initial Investment in Equipment
Sublimation requires specific equipment, such as sublimation printing, special inks, and heat presses that can maintain precise temperatures and pressure.
This equipment represents a significant upfront cost, which can be a barrier for small businesses or individual artists just starting out..
Additionally, the maintenance of this equipment, including regular calibration and potential repairs, adds to the ongoing expenses.
Learning Curve
Mastering sublimation on vinyl is not immediately intuitive. The process involves a nuanced understanding of temperatures, pressure settings, and timing, which can vary based on the type of vinyl and the desired outcome.
Mistakes can be costly, leading to wasted materials and time. Therefore, significant practice and experimentation are often necessary to achieve consistently high-quality results.
Comparing Sublimation on Vinyl with Other Techniques
Sublimation vs. Vinyl Heat Transfer
While both techniques involve transferring designs onto vinyl, the methods and outcomes are quite different:
- Deeper Color Penetration: Sublimation ink becomes part of the substrate, resulting in deeper, more vibrant colors that are more integrated into the material. This contrasts with vinyl heat transfer, where the design sits on top of the material and can peel or wear off over time.
- Durability: Sublimation provides a print that is more resistant to environmental factors such as UV rays and moisture. This makes it ideal for outdoor applications where longevity is critical.
- Quality of Finish: Sublimation generally offers a smoother finish without the feel of an additional layer on the surface, which is common with heat transfers.
Advanced Techniques in Sublimation on Vinyl
Mixed Media Applications
Incorporating elements such as screen printing, embroidery, or even other forms of digital printing with sublimation on vinyl can create multi-textured, multi-dimensional effects. These techniques can be used to add depth to the design and to differentiate products in a competitive market.
Special Effects
Adding special effects like glitter, metallic finishes, or glow-in-the-dark inks can elevate the aesthetic appeal of sublimated vinyl products. These effects require additional materials and steps but can result in eye-catching products that stand out to consumers.
Layering Techniques
Layering multiple colors or patterns through sequential sublimation processes allows for the creation of complex, vibrant designs that are not achievable through a single pass. This technique, however, requires precise alignment and timing to ensure high-quality outcomes.
Conclusion
Sublimation on vinyl blends innovation with creativity, allowing for vibrant, durable designs that integrate directly into the material.
Although it requires specialized equipment and knowledge of heat settings and material compatibility, the investment pays off.
Sublimated products are notably durable and resistant to fading and peeling, making this method ideal for high-quality, long-lasting applications.
For designers and businesses eager to master this technique, sublimation on vinyl offers extensive possibilities for customizing products with exceptional detail and color fidelity.
Frequently Asked Questions
Can any vinyl be used for sublimation?
No, only vinyl that can withstand high temperatures is suitable for sublimation. This usually involves specially coated vinyl designed to handle the heat and allow effective ink transfer without damage.